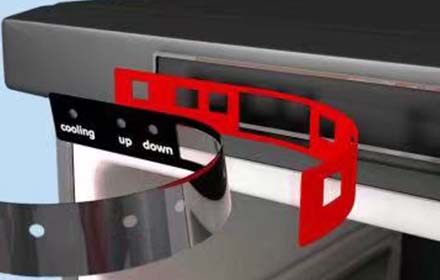
PE, short for Polyethylene, is the simplest structural polymer organic compound and the most widely used polymer material for protective films. It is made by polymerizing special polyethylene (PE) plastic films as substrates, and it can be divided into high-density PE, medium-density PE, and low-density PE protective films according to their different densities. Its properties include flexibility, good adhesion, easy application, easy-peeling, and residue-free removal.
The biggest advantage of PE protection film is to protect the product from pollution, corrosion, scratches, and maintain the original smooth and shiny surface during production, transportation, storage and use, thereby improving product quality and market competitiveness.
The application fields of PE protection film include stainless steel plates, aluminum plates, aluminum alloy profiles, plastic-steel profiles and doors and windows, aluminum-plastic panels, fluorocarbon panels, mirror panels, sandwich color steel panels, fireproof panels, decorative panels, organic glass panels, PS, PE, PVC board, polycarbonate board, security doors, signs, coated glass, high-end furniture, high-end crafts, electrical cabinets, computer cases, automotive lamps, flooring, household appliance shells, instruments, and various other areas where product surfaces need protection.
TPU and PU are mainly used in shoes and bars, so we will not elaborate on them here.
PE: that is, polyethylene, is widely used in the protective film industry. Its characteristics are: low price, flexibility, good stretch, environmentally friendly and pollution-free. Most products of this type have passed the ROHS environmental pollution test in the European Union. The disadvantage is poor weather resistance, and this material is not suitable for use in high temperature environments, generally below 60 degrees.
PVC: polyvinyl chloride, its characteristics are: good flexibility and better weather resistance (SPVC). The disadvantage is that it is not environmentally friendly, so many international big brands rarely use this material. This product is mainly used for anti-static protection and wooden speaker surfaces.
PET: polyester, its main characteristics are: good weather resistance, can withstand high temperatures of 100-150 degrees, good hardness and smoothness. The disadvantage is that it cannot be used on products with angles or corners and is mainly used for die-cutting.
PP: polystyrene, its characteristics are: it combines the characteristics of PE and PVC, is flexible, heat-resistant, and environmentally friendly, and is mainly used in the LCD industry.
Acrylic adhesive: widely used, good transparency and stability. However, differences may occur with time and environmental changes, such as decreasing adhesion over time.
Rubber: mainly used for black and white films, blue films, metal stamping, and other industries in the steel plate industry. Its main advantages are fast bonding speed and smoothness. The disadvantage is that it has more impurities and a short shelf life.
Silicone adhesive: high price, heat-resistant. The disadvantage is that the film may separate during use. Mainly used for scratch-resistant products.
Material Composition
PP (Polypropylene) and PE (Polyethylene) films are made from different types of polymers. PP film is produced from the polymerization of propylene monomers, while PE film is made from the polymerization of ethylene monomers. These differences in molecular structure result in distinct physical properties, such as strength, flexibility, and clarity. PP film tends to be stiffer and more rigid, while PE film is more flexible and softer, catering to different needs in packaging and manufacturing applications.
Strength and Durability
PP film is stronger and more durable compared to PE film. It has higher tensile strength and better resistance to heat, making it suitable for applications that require sturdiness, such as in industrial and food packaging. PE film, in contrast, is more flexible and tear-resistant, making it ideal for applications where flexibility is important, like shrink wrapping or protective covers. However, PP film’s rigidity makes it less prone to stretching or deforming under stress.
Clarity and Transparency
PP film generally offers superior clarity and transparency compared to PE film. This makes it ideal for packaging applications that require clear visibility, such as product packaging and labels. The clarity of PP film allows consumers to see the contents clearly, which is crucial for marketing and presentation. On the other hand, PE film tends to be more opaque, which might not be desirable in situations requiring visibility but can be beneficial for items that need some protection from light.
Temperature Resistance
PP film is more heat-resistant than PE film, withstanding temperatures of up to 120°C (248°F). This makes it suitable for high-temperature applications, including those involving food packaging that requires heat resistance or industrial uses where the material must endure exposure to heat. PE film, in contrast, typically performs well up to about 80°C (176°F) and is better suited for low to medium-temperature applications. The lower heat resistance of PE limits its use in some applications that require higher temperature stability.
Sealing Properties
PE film is easier to heat-seal compared to PP film. Its lower melting point allows it to bond easily when subjected to heat, making it ideal for packaging applications that require sealing, such as food packaging or shrink wrapping. PP film, however, has a higher melting point, requiring specialized equipment to seal effectively. While it offers more rigidity and durability, PP’s sealing properties can make it more challenging to work with in certain packaging processes where a strong, quick seal is needed.
Environmental Impact
Both PP and PE films are recyclable, but PE film is generally considered more environmentally friendly. The production of PE has a lower environmental impact compared to PP, as it requires less energy during production. Additionally, PE is more widely accepted in recycling programs, making it easier to reuse and repurpose. PP film, while recyclable, is less commonly recycled and may not break down as efficiently in some regions, which can increase its environmental footprint, especially in large-scale applications.
Cost
PE film is typically less expensive than PP film. This is due to the lower production cost of polyethylene and its wider availability. As a result, PE film is often chosen for cost-sensitive applications, such as basic packaging, shrink wraps, and plastic bags. PP film, being more durable and heat-resistant, tends to be more expensive, making it more suitable for higher-end applications where its superior strength and temperature resistance are necessary. However, for general-purpose use, PE remains the more cost-effective option.
Feature | PP Film (Polypropylene) | PE Film (Polyethylene) |
Material Composition | Made from propylene monomers, more rigid structure | Made from ethylene monomers, more flexible |
Strength and Durability | Higher tensile strength, more rigid and durable | Flexible, tear-resistant, but less durable |
Clarity and Transparency | Higher clarity and transparency | Less clear, more opaque |
Temperature Resistance | Can withstand higher temperatures (up to 120°C) | Lower temperature resistance (up to 80°C) |
Sealing Properties | Requires specialized equipment to seal | Easier to heat-seal, suitable for packaging |
Environmental Impact | Less eco-friendly, harder to recycle in some areas | More eco-friendly, widely recyclable |
Cost | Generally more expensive | More cost-effective, cheaper for mass production |