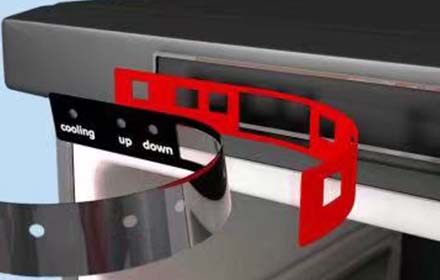
BOPP tape, or Biaxially Oriented Polypropylene, is a specialized tape that offers a higher level of adhesion, durability, and even tear-resistance. This tape is often used to seal, package, and secure goods, so it is vital that it has the highest quality when it comes to manufacturing. With this in mind, it is important to explore how the manufacturing process of BOPP tape impacts its end-result quality.
The creation of BOPP tape is a multistep process that involves several steps to ensure its ultimate quality. To begin, the polypropylene film needs to be extruded to form thin, even sheets of plastic before it can be sent to the adhesive lamination line. Once the sheets are ready, an adhesive is applied to the sheet for adhesion. After this, the sheet is passed through several rolls that cure and bond the adhesive to the BOPP tape.
The next step in the process is to print the tape with design patterns, logos, or other visuals. This is added via rotogravure printers that use photographic cylinders to transfer the pattern to this type of PP adhesive tape. The sheet then goes through one last lamination process, where it is cured and heat-sealed. This finishes the creation of the tape, and it is now ready for conversion into specific packaging solutions for transportation, retail, and other industrial purposes.
Quality control is an essential component of manufacturing BOPP tape material. To ensure the highest quality possible, manufacturers often monitor the entire fabrication process, from start to finish. This is done to make sure that all steps are correctly followed and the end product fulfills its expected function. Quality control allows for quality assurance, which helps businesses and consumers have peace of mind when it comes to their tape purchases.
Quality assurance brings a multitude of benefits for both consumers and businesses alike. By having a stringent quality control system in place, manufacturers are able to produce long-lasting products that can remain durable and strong for longer periods of time. This not only ensures the active life of the tape, but it also protects against any unpleasant or unexpected surprises when it comes to its reliability.
Additionally, quality assurance can prevent costly mistakes that can arise from defective tape. It also increases customer satisfaction, as buyers can be more confident that the product they receive will function at optimal levels. This enhances the overall manufacturer-consumer relationship, allowing customers to trust the product they are purchasing.
BOPP tape is an essential product for any industry, as it provides a long-lasting solution to securing and packaging goods. The manufacturing process of this tape is key to its ultimate quality and reliability, which is why quality control must be monitored and implemented for optimal results. By having strict quality control, businesses and customers can benefit from the assurance that all BOPP tape will be of the highest quality.
Adhesive Strength Test
The first step in assessing the quality of BOPP tape is testing its adhesive strength. A high-quality tape should adhere firmly to various surfaces without easily peeling off or leaving residue when removed. To test, apply the tape to different materials, such as cardboard, plastic, or metal, and peel it off. If the tape does not stick securely or comes off easily in a short time, it indicates poor adhesive quality, making it unsuitable for long-term use in packaging。
Tensile Strength and Tear Resistance
A good-quality BOPP tape should have strong tensile strength and tear resistance. It needs to withstand a certain amount of pulling force during use. You can manually stretch the tape to check if it tears easily. Premium tape will not break easily under stress and will maintain its integrity without splitting or fraying when torn. This makes it durable for packaging, reducing the risk of damage during handling.
Thickness and Uniformity
The thickness of BOPP tape plays a critical role in its durability and adhesive performance. High-quality tape typically has a consistent thickness that ensures durability and a strong bond. Measuring the tape’s thickness with a caliper can help assess this. The adhesive layer should be evenly spread across the tape, without noticeable variations or air bubbles. A tape with uniform thickness performs more reliably and is less likely to cause issues during application.
Clarity and Surface Finish
A good-quality BOPP tape should have high clarity and a smooth surface. Holding the tape against light allows you to inspect its transparency and smoothness. Premium tape appears clear, without bubbles, wrinkles, or cloudy spots. Low-quality tape may show signs of unevenness, such as a whitish appearance or imperfections. Clear and smooth tape not only looks better but also indicates good material quality and manufacturing standards.
Holding Power and Shear Resistance
The holding power and shear resistance of BOPP tape determine its long-term performance. To test this, apply the tape to a vertical surface and hang a small weight from it. High-quality tape should be able to hold the weight for an extended period without slipping. Poor-quality tape may lose its grip quickly, compromising the reliability of your packaging. Tape with good shear resistance will also maintain its adhesion when exposed to horizontal forces, ensuring strong and secure seals.